ABB transforms AMR performance with launch of Visual SLAM technology
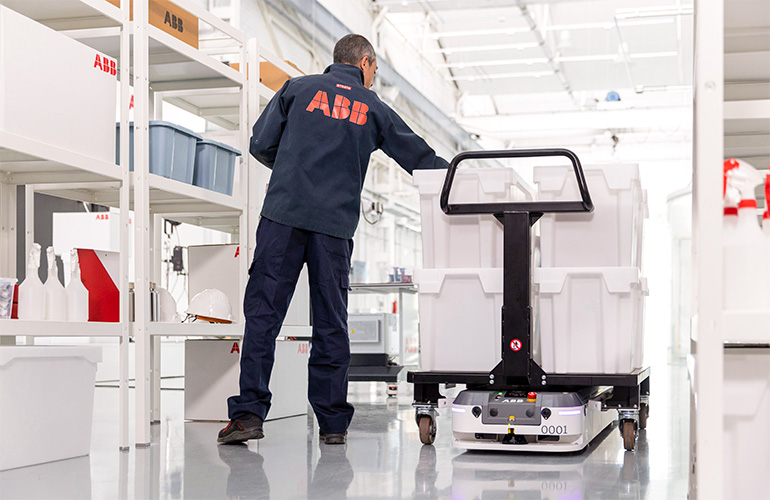
Visual SLAM enables AMRs to navigate effectively in complex working environments. | Credit:ABB
ABB Robotics is adding Visual Simultaneous Localization and Mapping (VSLAM) technology to its Autonomous Mobile Robots (AMRs). This enables ABB AMRs to make intelligent path-planning and obstacle-avoidance decisions based on their surroundings.
VSLAM uses AI algorithms together with the data from 3D vision cameras to perceive the world around the AMR in a three-dimensional representation. VSLAM has many benefits over other ways of navigating, like magnetic tape or QR codes which need more infrastructure to function properly. SLAM-based navigation techniques reduce commissioning time by up to 20 percent, requiring less calibration and no change to infrastructure.
Compared to 2D SLAM technology, VSLAM creates a three-dimensional view of the world. This ensures that the AMR can see overhangs such as shelving, drawers, walkways, cables, fork truck forks and other obstacles that are above ground level. Without this information, or additional onboard sensors, a 2D SLAM-based AMR might crash into these types of obstacles.

This close-up shows the front-facing location of new 3D vision cameras that are used for image capture of the environment in front of the vehicle. | Credit: ABB
2D SLAM is the current state of the art for AMR perception today. AMRs that leverage a 2D LiDAR perceive a 2D “slice” of the environment surrounding the AMR, typically at a height somewhere between 2” to 12” (50 mm to 305 mm) above ground level (the location of the LiDAR sensor).
“Our introduction of Visual SLAM AMRs radically enhances companies’ operations, making them faster, more efficient and more flexible, while freeing up employees to take on more rewarding work,” said Marc Segura, President of ABB Robotics Division. “Offering more autonomy and intelligence, our new AMRs operate safely in dynamic, human-populated environments. Visual SLAM technology provides a new level of intelligence for AMRs that transforms robotic applications, from production and distribution through to healthcare.”
VSLAM creates a real-time 3D map of all nearby objects and the perception algorithms provide a similar understanding to how human eyes perceive the world. VSLAM-based AMRs can see the floor, walls, and ceiling. It can also distinguish objects like humans, support beams, conveyors, fork trucks and even other AMRs. The solutions are capable of providing 0.1” (3 mm) accuracy.
Vision cameras are also much less expensive than rotating mirror LiDAR sensors, which helps reduce the overall cost of the AMR. The cameras have no moving parts, which also makes them more robust than a LiDAR unit, especially for a moving platform like an AMR that experiences vibrational shock from every crack and seam in the building’s concrete floor.
A downside of using 3D VSLAM over 2D SLAM, however, is that the perception algorithms are more computationally intensive, which means that the system requires more powerful edge computing onboard, and typically requires more power consumption. Battery management and utilization are of critical importance to a battery-powered mobile device like an AMR. But the benefits of improved perception performance outweigh any increased battery consumption for most ground-based mobile robots.
ABB developed Visual SLAM AMRs in collaboration with partner Sevensense Robotics, a provider of AI and 3D visualization technology. ABB’s latest AMRs, the AMR T702V, and AMR P604V, will implement the technology in Q3 and Q4 2023 respectively. More VSLAM-based AMR solutions from ABB will follow until 2025.
ABB acquired ASTI Mobile Robotics in July 2021, paying $190 million for the Spanish company. The ASTI headquarters is now the worldwide development center for ABB’s mobile robotics division. We talked to Sami Atiya, CEO of ABB Robotics and Verónica Pascual, CEO of ASTI Mobile Robotics to get their insights on the acquisition in episode 48 of The Robot Report Podcast.
The post ABB transforms AMR performance with launch of Visual SLAM technology appeared first on The Robot Report.
from The Robot Report - Robotics News, Analysis & Research https://ift.tt/XMiIkrb
via artificialconference
Comments
Post a Comment